- Merl - My T90 rebuild is finally done, and I must say that it went along much easier than I had expected. I used Rick's rebuild guide and a blowup picture for part name reference, never even looked at the shop manual for instructions on the rebuild. Overall, I'll give Rick's manual a hearty recommendation.
- This transmission is completely rebuilt with new bearings, seals, gaskets, cluster shaft, synchros and all small parts. Core charge $200. Side shift is applicable to the FC-150′s. Side shift Core charge is $200. Shift towers are available separately for $50. 4 cylinder top shift 500.00. 4 cylinder side shift 550.00. 6 cylinder top shift 550.00.
- T90 Transmission For Sale
- T90 Transmission Assembly
- T90 Transmission And Transfer Case
- T90 Transmission Rebuild
- T90 Transmission Adapter
- T90 Transmission Shift Tower Rebuild
LastUpdated November 12, 2005You can find the rest of my web pageshere
T-90 Rebuild Guide
4WD / 4X4 Truck & Wagon with T90A-1 Transmission Motor / Transmission Mount - F-4 134 473/475 (2WD 1946 to 1955) / F-6 161 685 / L-6 226 / T90A-1 & T96 Transmission Mount 1947 to 1955 Our Price: $18.00.
The T-90 Rebuild Video can now bepurchased here
Sorry, if you wanted the Model 18 Transfercase Rebuild Guide you willneed to go to: Here
In my search for detailed instructions for rebuilding a T-90 I found there was littlein the way of helpful information available. I did find a local transmission guru toanswer some of my hardest questions. Since I considered the service manual to beinadequate for a beginning rebuilder, I bought a T-90 and practiced taking it apart andputting it back together again. I have practiced it so many times now that I've lostcount, so I feel somewhat qualified to pass on what I have learned.
As other people use these instructions and provide me with feedback I will post theircomments. Merl was my first guinea pig and he, Rick Grover(http://www.public.asu.edu/~grover/willys), Frank Woods, Dr. Vern, Mike, Paul and numerousothers have provided some great feedback. Matt Clark was nice enough to provide me with atypo corrected copy of this page. I have also taken the liberty of taking a quotefrom one of Richard Needham's WillysTech postings about sealed bearings.
I can be reached for comments at rick48cj2a@satx.rr.com
Dr. Vern -
Merl - My T90 rebuild is finallydone, and I must say that it went along much easier than I had expected. I used Rick'srebuild guide and a blowup picture for part name reference, never even looked at the shopmanual for instructions on the rebuild. Overall, I'll give Rick's manual a heartyrecommendation. I'm doing this from memory so I hope I'm not leaving anything out, buthere are the more notable points and observations that I encountered...
As for my original problem...
T-90 shifts easily into R & 1st, never grinds at all even while rolling. However,after getting warmed up 2nd and 3rd would grind unless I shifted really slowly. The mainproblem was the worn 3rd gear synchro riding up too high on the surface of the input shaftbevel. The rear face of the synchro was scored where it had been hitting the small teethof the input gear. But the *cause* of this looked to be the two shims between the rearshoulder of the mainshaft and the bearing spacer. I don't see these type shims in the shopmanual (early Universal Jeep) and Rick said he hadn't come across them either. They sitbetween the shoulder of the mainshaft and the bearing spacer. They are cupped a little sothat the outside circumference points in toward the large sliding gear (1st/R). Mytransmission had two of these. My local parts guy, Leo, said that while not typically usedthey are used to adjust the mainshaft play. He said that the idea was to align the rearface of the bearing spacer with the rear face of the bearing adapter. When installed, youwant the rear faces of these two pieces to be flush. Any misalignment should be on theside of not enough shims rather than too many. It seems that the inside ring of the rearbearing rests on that spacer. Too many shims between the shaft's shoulder and the spacerwould cause the 3rd gear synchro to ride too close to the beveled input shaft all the timecausing premature wear. That's my theory anyway. When I put it back together I did a testfit before I put the rear bearing on and decided to not put a shim back in there. Anothertheory I have about this is that the tighter than normal mainshaft was allowing the smooth1st/R shift. Maybe a sort of automatic double-clutch thing happening in there.
T90 Transmission For Sale
SBart79631 wrote: I would suggest that every time the tranny is removed or rebuilt,that the bronze bushing in the center of the flywheel be replaced. This is an inexpensiveitem and not too much more work to do. The worst thing in the world is to rebuild thetrans and have it go bad again in a couple hundred miles cause the input shaft is wobblingall over, take it from me, I learned the hard way. Also, in the excitement of completingthe job, a friend forgot to fill her up with gear lube and drove it around the block, andright back up on the jack stands. Steve, 46cj2a restoration in 1972, currently working on48 cj2a
I agree with Steve on this. I've had several folks that have rebuilt their T-90s, onlyto still have the same problem with gears grinding during the 2nd and 3rd up-shift. Aftergoing back and replacing the crankshaft pilot bushing, the problem went away.
Mike Harris wrote:
First, the tranny was apart when *I* got there, and I think Joe said he'd gotten thetranny and transfer case from separate sources, and already in pieces. I could be wrong,though. Not being there for most of the disassembly was a major hindrance to reassembly aswe had to figure what went where from a poor-quality exploded drawing.
Joe also got a big box of extra/duplicated parts, which really came in handy. Itallowed us to evaluate each piece side-by-side and pick the one in best shape, creating a'franken-tranny.' No oil collector was in the tranny but we had one in the'spares,' may have been damaged because we had to grind off a little bit of thelip at the top to accommodate the mainshaft.
General comment - Rick practiced several times before the real deal. We didn't practiceand I think that if you skip this step, you should plan for and expect that you will beforced to 'practice' or redo at least a couple of times before it all comestogether perfectly.
To avoid confusion I recommend:
(1) Make sketches/notes of difficult assys, especially 2/3 gear hub & synchros& rear bearing. Every piece in the gearbox goes in 1 way and memory just wasn't goodenough, for me at least, even just a few hours later.
(2) Keep old/new parts separate.
(3) Lay out all parts in assembly order.
A separate section at the end of this instruction covers the Shift Tower. You canget there quickly by clicking Here
Special Tool Manufacture
1a. Tool A is manufactured using a 3/4' wooden dowel rod. Cut it to 6 7/8'long. If the dowel rod has a rough finish, it should be sanded smooth and the ends lightlyrounded. I did this using a 2' long drywall screw mounted in my drill. I turned onthe drill and screwed the screw into the end of the rod, as soon as it snugged up, the rodwas spinning nicely. It made sanding very easy.
Merl - Make sure you test fitthe dowel through the front and rear holes of the case prior to assembling the clustergear, sanding was required in my case.
Also check to insure that the shaft is not too long to fit into the case from theinside.
2b. Tool B is manufactured using a length of 1' diameter
Merl - Look for conduit labeled3/4'. You might have to buy a long piece, but it's dirt-cheap. Exact measurement ofthe electrical conduit tools is not critical. Within 1/4' inch of Rick's measure isOK, but do make sure there are no burs on the end of the tool.
Ok, folks here's the skinny on this electrical conduit. The correct size is as Merldescribed 3/4', however, you will find that when you measure 3/4' conduit it is13/16' inside diameter and 15/16' outside diameter. I hope this clears up theconfusion. In addition, Merl is also correct about the length of tools A, B, and C. Theyare going to be used as spacers to hold the needle bearings in place during assembly, solength is not critical.
2c. Tool C is manufactured using a length of 1' diameter electrical conduit. Cutit to 1 7/8' long with a hacksaw. It must be cut straight and any burs removed.
2d. Tool D is manufactured using a length of 1' diameter electrical conduit. Cutit to 1' long with a hacksaw. It must be cut straight and any burs removed.
2e. Tool E is manufactured using a 3/4' wooden dowel rod. Cut it to 2' long.The dowel rod must be sanded to slightly less than 3/4' and will most likely bedestroyed in this use. You could also make it from a piece of brass rod but I used thewooden dowel since I already had some left over.

Other Tools I Used
Brass Drift (any size will do but the bigger the better up to 1/2')
Set of 12 point 1/4' drive sockets (I've been told that some of the bolts areAllen headed instead)
Pair of flat bladed snap ring pliers . Roundtipped pliers will not work.
Frank - Get the right tool toinstall the snap rings. The small stiff one on the front, the main-drive-gear snap ring,is a pain in the ers. Jabbed my finger with it trying to pry it out the first time.
Wooden board (I used a 2' X 12' X 24' but size really didn't matter muchhere)
Work bench (I tried to rebuild it on the floor of the basement but found the work bencheasier.)
Ziploc bag and Stove top (These are replacing my old 'freezer technique' forthose of you with early copies of this guide.)
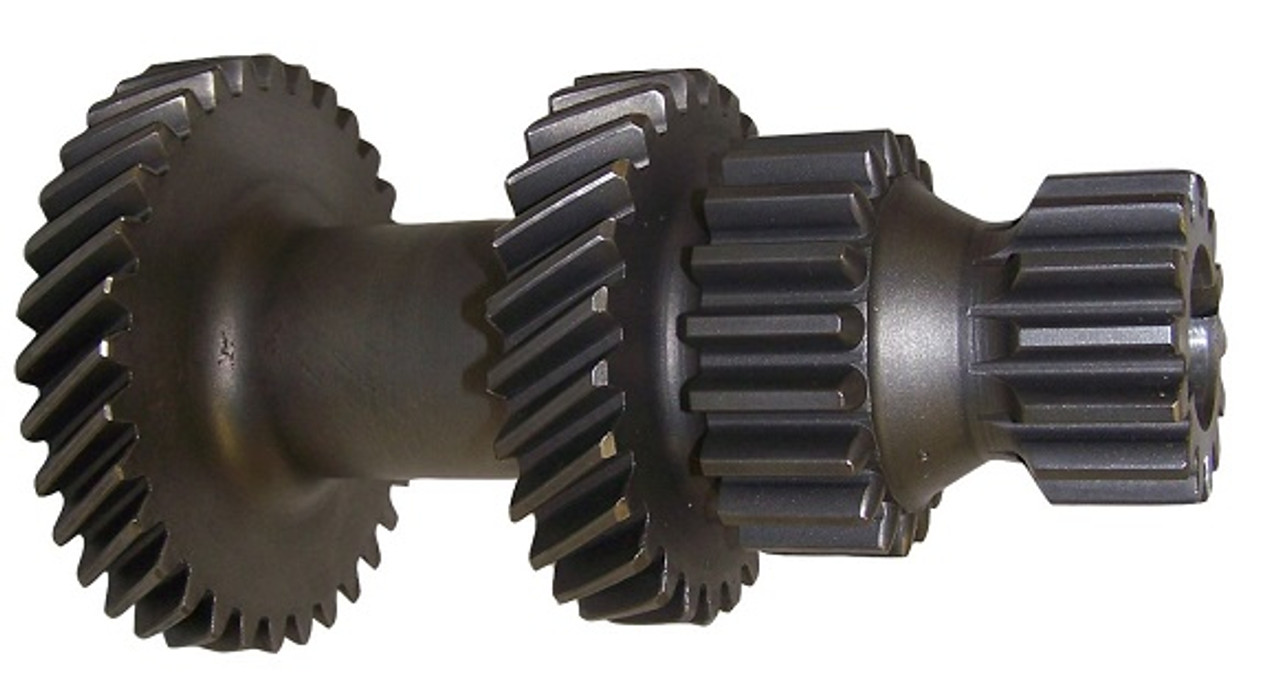
Small brass hammer (A small plastic mallet would probably work just as well)
5' C-Clamp (Optional)
If still attached to the transfer case you could possibly need two long thin woodenwedges 5' long, tapering down from 1' should do.
Disassembly
2a. If the transfer case has already been removed proceed to step (2h). Remove screwsfrom transfer case rear cover. Or, if equipped with a PTO or Warn OD remove screws andremove the PTO or OD from transfer case.
2b. Remove transfer case bottom cover .
2c. Remove the cotter pin, nut and washer. (You may noticein the picture that the two gears do not mesh. That's because they are not a matched set.The intermediate gear is for a 26-tooth output and the output gear shown is a 29-tooth.They don't even fit together enough to install the intermediate shaft in thetransfer-case. I just set it in place so the view would look close to what you would seeif you were just opening up the case. If you have difficulty removing the nut you canwedge a hardwood block or brass drift between these two gears to lock them into position.Once the nut and washer are removed the main gear can be removed from the main shaft. Ifit sticks two thin wooden wedges can be tapped in between the rear bearing and main-gearto pop it loose.)
2d. If the shift tower has been removed while removing the transmission proceedto step (2e). Shift the transmission into neutral, remove the six screws from the shifttower and remove it.
2e. To hold the mainshaft in place until removal is desired, install the front twoshift tower screws back into their holes. Loop a heavy piece of wire under and behind thesecond speed gear and tightly wrap it around each of the two screws .
2f. Remove the transmission to transfer case bolts
2g. Separate the transfer case from the transmission.
2h. Remove the three screws from the main drive gear bearing retainer.
2i. Remove the retainer, seal and gasket.
2j. Remove the two twelve point/socket head screws that hold the oil collector to thecase. (The oilcollector can not be removed at this time so move it out of the way of the main drive gearas needed.)
2k. Tap the main drive gear forward about 3/8'. (Do not try to drive the main gearout at this time or it will damage both it and the cluster gear.)
2l. Remove the wire and screws from the case and mainshaft that you installed in step(2e).
2m. Slide the clutch sleeve forward on the mainshaft.
2n. Slide the mainshaft complete with the front synchronizer blocking ring backwards,then tilt the front end upward to clear the cluster gear
Merl - Disassembly was easy, thehardest part was getting that locking plate out of the slots on the rear of the twoshafts. As Rick mentioned, mine was inserted from the top down and I couldn't get the rearbearing adapter plate off without first removing this plate. I bunged up the plate reallywell and wound up getting a replacement for it.
2o. Using Tool A or a brass drift, gently tap the countershaft toward the rear of thetransmission about 1/2'.
2p. Then using a brass hammer also tap the idler gear shaft toward the rear of the caseenough to free the locking plate. In some cases this will be impossible and you will havedrive the locking plate out of the reverse idler shaft.
2q. Remove the locking plate.
2r. Using tool A drive the countershaft out of the cluster gear.
Rick Grover - When you say todrive the counter shaft out, it should be driven out to the rear. The front hole is a fewthousandths smaller that the back hole. Driving it out the front would be much harder andcould stretch the front hole.
2s. Drop the cluster gear into the bottom of the case.
2t. Tap the main drive gear forward and out of the case.
2u Remove the oil collector.
2v. Remove the countershaft cluster gear.
2w. Remove the thrust washers from the case.
2x. Collect the pilot bearings and put them aside. (There is a set of needle bearingsknown as pilot bearings that fit inside the main gear. These bearings are much larger thanthe bearings used in the cluster gear. The nipple on the front end of the mainshaft rideson these bearings, and they usually fall into the bottom of the case when the mainshaft isremoved.)
2y, Using tool E drive the reverse idler gear shaft out the back of the case. (This must be done from inside the case. Caution: do not attempt to drive the shaft intothe case from the rear as this can damage the shaft and the case. Remove the reverse idlergear from the case. Some people have found it necessary to use a bent piece of rebar todrive the reverse idler gear out of the case. Use as little force as you can to preventdamage. Whatever you do, don't drive the shaft into the case.)
(Here is a helpful tip. When driving out the reverse idler shaft, stand the case on itstail end. To do this, place a 3/4' deep-well socket over the end of the shaft, andplace 3 more deep-well sockets around the bottom to provide good balance. Have a secondperson hold the case in place and drive out the shaft. This was much easier than trying tohold the case in place laying flat.)
Mike Harris wrote: Reverse idlerwas a bear. We pounded it out using all-thread since it was long & flexible enough toget around the slight bend from the front of the case to the shaft.
(Danny M. has provided us with an alternative method of removing the reverse idlershaft. Use a 4 inch C-Clamp, a 3/8' drive 1/2' socket and a 3/8' drive3/4' deep-well socket. Install the C-Clamp as shown withthe 1/2' socket against the inside end of the idler shaft and with the deep-wellsocket slid over the outside end of the shaft. It took a good bit of pressure and a coupleof taps on the threaded end of the 'C' Clamp. Then you tighten it again and tapit again until the inside end of the C clamp bottoms out. Once it breaks free it caneasily be driven out the rest of the way with your drift)
I think Danny has a great deal more patience than I have. I had a really stubborn shaftthat I tried to remove this way and I ended up breaking my C-Clamp. Now mind you, fromstart to breakage only took me 5 minutes. I was using a cheap C-Clamp of very poor qualityso here's what I suggest. If you are going to use Danny's procedure, use the largest,highest quality clamp you can fit into the case and take your time. Danny's clamp looks alot better than the one I was using and he's already proven it can be done. So have funand if you use this method please let me know how it goes.
2z. Remove the main bearing snap ring using flat edged snap ring pliers.
2aa. Hold the main drive gear by the bearing and gently tap the small end of the shaftonto a board until thebearing slides down and off the gear shaft
Rick Grover - An alternative isseveral taps with the brass hammer. Worked for me. :-)
2bb. Remove the front bearing washer noting the direction the lip fits on the bearing.
2cc. Slide the clutch sleeve off of the clutch hub, making sure not to drop the threesynchronizer plates . (Collectthe synchronizer plates and put them off to one side for inspection.)
2dd. Using flat edged snap ring pliers remove the clutch hub snap ring.
2ee. Remove the clutch hub from the mainshaft.
2ff. Remove the synchronizer springs from the hub.
2gg. Remove the rear blocking ring from the mainshaft.
2hh. Remove the second speed gear from the mainshaft.
2ii. Merl has described a shim installed behind the second speed gear on his mainshaft.My transmission did not have this shim and the parts listing does not show it. It seemsthese were installed to bring worn out parts into proper tolerance. If you have this shimremove it now.
2jj. Remove the rear bearing from the mainshaft. If necessary, stand mainshaft on itstail end an use the 1st/Reverse gear like a slide hammer to drive the rearbearing off the shaft
2kk. If you have the large hole bearing adapter, remove the snap ring from inside thebearing adapter. (Youcan not use snap ring pliers to remove this snap ring. A flat bladed screwdriver worksjust fine. Hook it under the notch in the ring and pry the ring out. Place the bearing onthe front end of the mainshaft again use a slide hammer action to drive the bearing fromthe adapter.
2ll. Slide Tool A, bearings, washers, and spacer from inside the countershaft clustergear. Disassembly is complete.
Cleaning and Inspection
3a. Thoroughly clean all parts with solvent. A good small parts kit will contain needlebearings, snap rings, synchronizer plates and springs, bearing spacer and thrust washers.Do not waste too much time cleaning these parts unless you want to use them to practicethe assembly and disassembly procedures. They should be examined to determine commonfailure items.
3b. The following inspection procedures can be used to determine which parts should bereplaced:
1. The main Drive Gear bearing should bereplaced if the center wobbles in the cage, grinds when spun or makes a squealing noise. Irecommend changing it anyway. This bearing may be changed with a sealed bearing but somethings need to be changed if you do this. Whatever bearing you choose, make sure that ithas the groove as shown in the picture. This is where the front bearing snap ring sits andit is used to hold the bearing in place.
Richard Needham - Well I made it out to the shop and found thebearing number for the front of the T-90 with the seal. It's a SKF bearing but any goodauto parts store should be able to cross reference to another brand.
SKF---6208-2RSNRJ/EM
Note: You must remove the seal from the inside of the bearing, to allow the 90W oil tolubricate the bearing. Also there is a drain-back hole in the front of the transmissionthat must be plugged if you use this bearing. When you remove the 3 Allen bolts to takethe cover off the front of the transmission, you will see there are 4 holes in thetransmission the one with no treads is the drain hole. Plug it with silicone or tap it anduse a small pipe plug. Otherwise the sealed bearing will do no good because the oil willrun out the drain hole.
I tried to locate the bearing that Richard used but was unable to find it. I did somelocal research and found this sealed bearing.
MRC brand Part #208-SZZG
I found them at Purvis Bearing in San Antonio (210) 299-1010. They cost $31.25 (At thetime I authored this July 2000) and they had them in stock. They said they would mailorder them to credit card customers. They also said to leave the seals installed on bothsides because the bearings were designed to run for over 100,000 miles without servicing.
Update: (Nov 2005) Mike Harris has reported paying $48.86 plustax for his bearing at the Purvis Bearing in Austin and I recently paid about $51 out thedoor here in SA. These beings have gone up a lot in 5 years.
I'm going to repeat at this time, If you are using this sealed bearing and you have thelong-shaft main-gear-shaft, you must plug the hole in the pilot bearing race to theoutside of the transmission or it will leak badly.
If you determine that you need a new Main Drive Gear Shaft make sure that you order theright one. I don't have the different lengths on hand but it you measure the length theyshould be able to tell you which one you have.
2. The front Bearing Washer should be replaced if bent or scored.
3. On the Main Drive Gear (Referred to by some as the Input Shaft) inspect thepilot-bearing race for scoring and pitting. Inspect all oil passages to insure they areclear. The inside diameter can be checked by measuring the diameter of the pilot shaft onthe Mainshaft adding this size to the twice the diameter of a new pilot needle bearing.The sum of these diameters should be within .001' of the inside diameter of the MainDrive Gear pilot bearing race. An easier way to check this is to install new bearings inthe race and insert the mainshaft into the bearing. There should be virtually no wobble ofthe shafts. If this fit is loose it will cause the pilot bushing in the engine crankshaftto wear out quickly. Check the gear teeth and blocking ring teeth for signs of wear andbreakage. The beveled surface the blocking ring rides on should be smooth and free ofcracks or pits . If anyof these items is damaged you should replace the Main Drive Gear.
Long Shaft and Short Shaft Main Drive Gears have been identified as being different inmore ways than just length. The long shaft has an oil hole drilled from the inside of thepilot-bearing race to the other side of the front main bearing race. It is the dark spotin the bottom as shown in the picture. It is easier to see in this photo taken from theother side. If you install a sealed bearing during installation, you must seal this holeor the transmission will leak.
4. Countershaft gear Oil Collector should be examined for cracks and dents. If damagedreplace it. Many people recommend leaving this assembly out of the transmission, but Irecommend against this. The Oil Collector retains oil around the front end of theCountershaft Cluster Gear. This feeds oil into the needle bearings. In the event that youran low on oil the collector would continue to feed oil onto the bearings. The OilCollector will also help to prevent the oil from foaming at high speeds. Note thedifference between the old oil collector and the new one.The new one at the bottom is not as good as the old one and will require trimming the edgeto get it to fit without dragging on main-gear. If you choose to buy a new oil collectormake sure you are ready to trim it if necessary.
5. The synchronizer blocking rings should be inspected for broken teeth and worn matingsurfaces. The mating surfaces that fit against the Main Drive Gear and Second Speed Gearshould have small grooves machined into them with raised surfaces that come to pointsbetween the grooves and should be free of cracks and chips
Merl - Inspection was also easy,just so long as you know what these things are *supposed* to look like. For example, Istated that my synchros looked good...*wrong*. I made this assumption without actuallymaking a side-by-side comparison to new synchros. Turns out that while my 2nd gear synchrowas ok, the 3rd gear was badly worn. Take your mainshaft assembly completely apart andtake a good close look at everything. With everything apart take your synchros and putthem on the beveled edge of the 2nd speed gear and the input gear. If either the bevelededge of the gear is worn or the rear or inside of your synchro is worn replacement isneeded. As Rick suggests, you might as well just go for new synchros, they're cheap.
6. The Clutch Sleeve should beinspected for cracks and pits. Inspect the inside splines for sharp edges and burs. Thesecan be removed with a file or crocus cloth. After cleanup, it should still fit snugly onthe clutch hub. If not replace it and the clutch hub.
Rick Grover - The burrs on theinside of the clutch slider were pretty bad on mine. I worried about them and whether ornot to replace it, but finally did as you recommended, filed them off with a fine file andemery cloth.
7. The Clutch Hub should beinspected for sharp edges and burs on the splines. Caution should be used when handling aused hub as it could have very sharp edges. Using a file or crocus cloth, remove any burs.Check fit on the Mainshaft and inside the Clutch Sleeve for snug fit. If it does not fitboth pieces snugly, replace it.
8. The Second Speed Gear should beinspected for broken or worn teeth. Examine the blocking ring surface area for scoring.Check for snug fit on main shaft. If it does not fit properly or if teeth are damagedreplace the gear.
Frankie Ladwigprovided us with this fine picture and some information from Jason at Mile High Jeep Rebuilders. Note thechevrons on the left gear as compared to the chevrons on the new right gear. Thesechevrons are what the clutch hub slide over to lock the tranny in second gear. Ifthese chevrons wear down too far, they do not allow the clutch hub a proper gripping areaand this can lead to the tranny pooping out of second. Second gears are expensive but ifyours is wearing down and been popping out of second I recommend you replace it.
9. 1st/Reverse sliding gear
10. The Rear Main Bearing should be replacedif the center hub fits loosely in the cage. Note that this bearing does not have a snapring groove like the front bearing does. I also recommend changing this one regardless.
11. Inspect the Mainshaft
12. The Countershaft Gear Set (Known by most as the Cluster Gear) should be examinedfor cracks and broken teeth. Because the 1st/Reverse gear rides well up ontothe 1st gear ring on the Countershaft Cluster Gear , you can have as muchas 3/8' of wear to the 1st gear ring without affecting the gear'soperation. Small chips and sharp edges should be dressed with a file. With newCountershaft Washers, and bearings installed, the cluster gear should have no wobble onthe countershaft. The easiest way to detect inside wear on the cluster gear is to run yourfinger inside and feel the surface. If you can feel ridges inside the gear, it is worn andshould be replaced.
13. The Countershaft should fitvery tightly into the case. It should also have no perceptible grooves or ridges worn intothe bearing surface. These shafts are cheap so do yourself a favor and replace it.
14. The Reverse Idler Gear will haveworn teeth. These should be dressed with a file to eliminate small chips or sharp edgesthat could be broken off and left inside the transmission. Check the fit on the IdlerShaft for wobble. The gear has a bronze bushing that should look like this . Ifit doesn't fit well or is missing large sections of teeth it should be replaced.
15. The Reverse Idler Gear Shaft should be inspected for chips or wear grooves. Sincethese shafts are cheap, if you suspect the shaft is worn then replace it.
16. The case must be thoroughly cleaned and inspected for cracks, giving extra care tothe bottom and around each case opening. Ensure the countershaft and reverse idler shaftfit very snugly into the case. Do not leave any old gasket material on the matingsurfaces. You will notice that as the years have passed, people have tried to seal theirleaking cases by tightening the screws tighter. This leads to the edges around thethreaded areas being pulled out from the case. This is no big deal except that it willkeep you from getting a good seal. Use a file to level the edges of the threaded holes.Make sure to keep the file flat and don't dig into the metal. Remember the intent is tolevel the surface again.
Frank - Buy your small partskit from:
Four Wheel Drive Hardware USA/Canada 1-800-333-5535
Int'l 1-330-482-4924 or 1-330-482-5560
Fax 1-330-482-5035
www.4wd.com
Columbiana, OH
It's the best.
Rick - I agree with Frank on this one. I've seen small parts kits from a lot ofdifferent places but the one from Four Wheel Drive Hardware is the most complete. By thetime you add the parts that the other kits don't have, the price is higher to buy fromanybody else. If this situation changes or somebody has a different experience please letme know.
Dr. Vern - Did any of thelater model T90's use a neoprene lip seal at the front? On mine, the front seal was a flatcork washer sandwiched against the face of the bearing by the bearing retainer. Thebearing that I removed (original?) was shielded, but not sealed, on both sides. Theshields were probably enough to slow the flow of oil to the point that the cork washercould handle it.
I had been pondering installing some sort of neoprene lip seal at the forward bearingretainer. These are those common type of seals used on the transfer case, timing chaincover, and other applications. I decided against it because the bearing retainer wasn'tthick enough. There was not enough material to cut away to press in a seal. Nor was thatpart of the input shaft smooth enough for a seal. I suppose I could have rigged up atoolpost grinder on the lathe, but the sealed bearing idea was looking a whole lotsimpler.
When I got my small parts kit home, I sorted through this wonderful mixture of needlebearings, thrust washers, gaskets and so on. (I kept picturing Merl's boys playing in thegrease.) The kit didn't have the cork washer, which I wasn't going to use anyway. Insteadthere was a small neoprene seal, sized to fit over the input shaft.
So one very long, not necessarily relevant story later: Did some later model T90's usea neoprene lip seal for the input shaft? It looks like the bearing retainer would have tobe different to hold it in place, and the finish on the shaft would have to be smoother. Idon't plan to add one, because it would soon fail anyway if there was no oil on the shaftdue to the sealed bearing. I'm just wondering, that's all.
Jason@MileHiJeep - We havenew T-90 bearing retainers that are machined to accept a metal/neoprene seal. When ourtech rebuilds our T-90's, he said that he polishes the input shaft to give a bettersealing surface.
Rick - If you are not installing a sealed bearing I highly recommend buying theseparts from Jason at Mile High Jeeps.
Rick
Assembly
Merl - I have to *highly*recommend Rick's technique using the electrical conduit. After I cut the tool A, B, C, andD and finally understood the way Rick's method works, I put newspaper on our kitchentable, got my 6 & 8 year old boys to count out 4 piles of 22 needle bearings each,gave them a cup of grease and let THEM put the thing together. Of course I supervised tomake sure everything was going in the right order, but the fact that my 6 year old didmost of the work should tell you how easy these tools make it (plus, my boys had a goodtime with the grease).
Mike Harris: Thedowel/electrical conduit for the countershaft needle bearing assy made a fussy job easy.This 'tool A, tool B, Tool C' cha-cha-cha is the way to go. Don't do it theconventional way unless you want to make yourself nuts trying to hold four rows of needlebearings in with grease (with both 6-7/8'-long index fingers), using the other handto hold the countershaft, your other hand to hold the plastic hammer, leaving your otherhand free to hold the shop light to watch yourself catch a needle bearing with thecountershaft & drive it sideways into the case.
4a. Install the Front bearing washer onto the main drive gear. This washer is a formfit washer and should be put on the shaft so that it will match the contour of thebearing.
4b. Install the main drive gear bearing onto the shaft with the snap ring slot forward.Grease the shaft before installing the bearing. This bearing is a press fit to the shaftbut it can be installed using the following method.
Mike Harris: We heated the front& rear bearings by putting in a Ziploc and putting the bottom end of the Ziploc intoboiling water - boil-in-bag-bearing, yum. This got the bearings hot enough that I don'tthink freezing was needed.
You must install the bearing onto the shaft in one quick motion or the bearing willcontract around the shaft. If the bearing fails to seat all the way onto the shaft you canpersuade it using a brass drift. Make sure to only tap on the inside edge of the bearingcage. If you use the outer edge of the bearing you could damage it.
Make sure the snap ring groove is forward or you will have to do it again.
4c. Install the snap ring onto the main drive gear using flat bladed snap ring pliers.(This snap ring holds the bearing on the main gear.)
4d. Install the front bearing snap ring on the outside of the front bearing using flatbladed snap ring pliers. (This snap ring holds the front bearing in the case.) You aredone with the Main Drive Gear for now.
4e. Assemble the Countershaft Cluster Gear assembly. At each step that says'install' during the assembly of the Countershaft Cluster Gear use a liberalamount of grease.:
4e1. Stand the cluster gear on its large end on top of piece of cardboard and insert Tool A into the hole.
4e2. Install Tool B and Countershaft Spacer over Tool A in that order.
Merl - Make sure you grease themiddle spacer...I forgot. But, I was able to put a little light oil in the lube hole inthe middle of the gear so I didn't take it all back apart.
4e3. Install one bearing washer over Tool A .
4e4. Install 22 needle bearings into the space left between Tool A and the Cluster Gear shaft.
4e5. Lifting the gear while holding the cardboard over the end, lay the cluster Gear on its side.
4e6. While holding Tool A in place, push the needle bearings into the shaft using Tool C and remove Tool B .
4e7. Again using the cardboard to hold the bearings and spacers in place, stand the Cluster gear onto its small end.
4e8. Install the 2nd bearing washer and 22 needle bearings .
4e9. Lifting the gear while holding the cardboard over the end, lay the cluster Gear on its side.
4e10. While holding Tool A in place, push the needle bearings into the shaft using Tool D and remove Tool C.
4e11. Stand the Cluster gear back onto its large end.
4e12. Install the 3rd bearing washer and 22 needle bearings, followed by the 4th washer.
4e13. Using the cardboard to hold the bearings in place, stand the Cluster gear one last time back onto its small end and remove Tool D (It may be necessary to insert tool B part of the way into the shaft to remove Tool D).
4e14. Install 5th bearing washer and 22 needle bearings, followed by 6th washer. This completes the assembly of the Countershaft Cluster Gear assembly.
Note: The last tranny I built had 4 washers of clearance left after installing the cluster gear bearings and washers. If allowed to ride like this the bearings can migrate and twist in the cluster gear. I added these washers into the count for the bearings. I never put more than two washers together in the buildup. This meant that once I found out how many washers were needed, I had to take it all back apart again to group the washers into pairs. The only thing I can think of that would have caused this, is a difference in manufacturing lengths for the bearings. I don't have a micrometer so I wasn't able to check this out. The key here is to get the bearings to fit firmly but not tight on the ends.
Frank - I didn't use any ofslick Rick's tool tricks. I'm wondering if someone else can verify if this works:
1. pack the bearings in the cluster gear, or let your kids do it.
2. grease up the countershaft washers and place them and the cluster gear in the bottomof the case, gently.
3. insert the main drive gear with its bearing, washer, snap rings and packed with theroller bearings into the front of the case.
T90 Transmission Assembly
4. gently lift the cluster gear and mesh its forward most gear with the main drivegear.
5. gently insert the countershaft through the back of the case and into the clustergear .
6. insert the mainshaft assembly through the back of the case and gently wiggle/insertinto the main drive gear
4f. Place the large thrust washer coated with assembly grease into position in thecase. It goes to the front of the case with the brass side toward the cluster gear.
4g. Place the small steel thrust washer heavily coated with grease in the case. Thesteel thrust washer has a steel tab that will sit on a shoulder in the case. This tabprevents the washer from spinning when the cluster gear rotates.
4h. Place the small brass rear thrust washer onto the cluster gear. Most cluster gearshave two notches cut into the small end for the thrust washer to fit into. The smallerthrust washer goes to the rear with the brass side toward the steel washer.
4i. Place the Countershaft Cluster Gear into the case withthe large end to the front. It will justlay in the bottom for now.
4j. Place the Oil Collector in position in the case. Donot install the screws at this time. You will note on the left side of the photo someextra parts that your T-90 doesn't have. This is the shift mechanism for the side shifttranny. You can build a side shift T-90 to be a top shifted T-90.
Frank - Don't forget to installthe oil collector in the right order because it won't go in last like I thought it would.Unless you want to practice disassembly/assembly one more time.
4k. Install the Main Drive Gear into case from the front.
Dr. Vern - I found it easierto install the pilot bearing rollers before installing the main drive gear. I have amagnet on a stick that worked great for handling those teeny little rollers, too. Thingsgot pretty slick using assembly lube.
Dr. Vern -Keep in mind whenyou put the main drive gear and its bearing in the front of the case, you will have toback it out partway later. Since I did the sealed front bearing mod, I decided to sealbetween the big snap ring and the case too. When I had to back out the bearing and shaftas required, the sealer had partially set and came apart in globs. I had to scrape itclean and reseal it. So if you plan to seal it like I did, wait until just beforeinstalling the bearing retainer to add the sealer. I also cut a piece from the snap ringof the old bearing, and used it to fill the gap in the new bearing's snap ring. Hopefullythis will help me get a better seal without that big gap. If you are not replacing thebearing, a piece of thin metal the appropriate size would work just fine. If you are usingthe stock front seal and open bearing, this will not be needed.
4l. Install the countershaft through the cluster gear from the rear of the case.
Dr. Vern - The rearcountershaft thrust washer gave me fits when it was time to lift the gear into place toinstall the countershaft. It kept staying down, not lining up. Then I looked at how thekeyed tabs were oriented. I had them aligned vertically at first. When I turned the gear90 degrees so the key tabs were horizontal, the thrust washer did not slip down as Ilifted the gear into place.
Rick - Some cluster gears do not have the slots cut into the small end for the tabs tofit into. If yours does not, you will need to either flatten the tabs or break them off.
4m. Place the reverse idler gear in position with the larger center hub boss pointingforward. Install Reverse Idler Gear Shaft from the rear of the case. Watch the position ofthe locking plate slot. Do not install the shaft all the way or you will not be able toinstall the locking plate.
4n. If you have the shimidentified by Merl and you wish to use it, install it on the mainshaft now. I feel thesewere only used to compensate for worn parts, so with all new bearings and blocking ringsyou should not need them.
4o. Install the second speed gear onto the mainshaft with the blocking ring matingsurface pointing forward.
4p. Place the rear blocking ring on the second speedgear.
4q. Install the synchronizer springs into the clutch hub. Theyshould be installed in opposite positions with one in the front and one in the rear. Oneend of each spring should fit into the same synchronizer slot. I have no idea why they areinstalled like this but every old transmission manual I have been able to find shows thesprings installed this way. If you installed them the other way, I don't think it wouldhurt but why fight 50 years of experience?
4r. Slide the clutch hub onto the mainshaft with the longer, narrow center boss pointedforward. This photo shows therear of the clutch hub with the shorter but wider boss. Some folks have confused thedirection of this hub during installation and this prevented the transmission from goingtogether. (Clarification for this step provided by Doug Karr)
4s. Install the clutch hub snap ring.
4t. Heavily grease the synchronizer plates and holdthem in place while installing the clutch sleeve over the hub. There are three slots inthe blocking ring that the synchronizer plates must fit into to install. Make sure theshift fork groove is to the rear of the mainshaft. It can go on the other way, but it willprevent you from installing the shift tower later.
4u. Stand the T-90 onto its front end with the main drive gear shaft hanging over theedge of the workbench.
4u1. Insert Tool A into the pilot bearing hole of main drive gear.
4u2. Grease needle bearings and insert them into the main drive gear.
4u3. Remove Tool A while rotating it.
4v. If you have the large-holebearing adapter you will now install rear bearing in rear bearing adapter and install snapring. This bearing is also a press fit and can be tapped in using a brass drift. Ifyou have the small hole adapter the bearing will just sit in an shallow relief in theadapter.
4w. Place the T-90 back down flat.
4x. Slide the main drive gear as far forward in the case as possible.
4y. Slide the clutch sleeve as far forward as possible without releasing thesynchronizer plates.
4z. Install the front blocking ring on the main gear with grease to hold it in place.
4aa. Install the mainshaft from the rear of the case and insert it into the pilotbearings. You will need to lift the front of the mainshaft up over the secondgear ring on the cluster gear and then allow it to drop into place in the pilot bearings.If you can't get it to go over the second gear ring, you don't have the clutch sleeve farenough forward on the mainshaft. The three synchronizer plates will need to fit intothe notches in the front blocking ring.
4bb. Slide the main drive gear back into case until outside snap ring is firmly againstthe case.
4cc. Install the screws in the Countershaft Cluster Gear Oil Collector.
4dd. Install the front bearing retainer gasket and bearing retainer oil seal if used.(Mine used a rubber seal installed in the bearing retainer.)
4ee. Install the bearing retainer and tighten screws.
4ff. Install the 1st/reverse gear onto the mainshaft with the shift forkgroove forward.
4gg. Install the rear bearing spacer on the mainshaft. (If you forget this part themainshaft will have too much free play.)
4hh. Install the rear bearing adapter with the bearing onto the mainshaft. This is alsoa press fit. I used a 2' piece of the PVC pipe to drive the bearing down onto theshaft.
Merl - The only other problem Ihad during assembly was getting the rear bearing pressed onto the mainshaft prior toinserting the mainshaft into the case. I tried Rick's 2' PVC pipe technique, but ittends to shoot small shards of plastic off into the bearing.

I wound up using a blunt nose chisel on the inner race, a tap on the chisel with ahammer at 90 degree increments around the bearing race did the trick.
Rick Grover - Brass hammer tapsworked for when I did my T-90, I never hit anything with steel. Get a brass hammer and/ora brass punch. They are about $10 each. They get all dinged up and even shed little brassflakes sometimes, but they do not scratch or mark the machined steel surfaces.
4ii. The mainshaft washer and nut may be placed on the mainshaft for safekeeping.
4jj. Install the countershaft and reverse idler gear shaft lock plate. I've found a lotof these are not made to specifications and need to be filed or ground down to fitproperly.
4kk. Tap shafts into case until the locking plate is held firmly in place.
Dr. Vern - The front bore of thecountershaft is known for leaking. The end of the shaft is about 1/16' inside thecase when fully assembled. I plan to put some sealer in there when I bolt the transmissionto the bellhousing. The flat surface of the bellhousing will sandwich the sealer in place.Naturally you don't want to use too much, but just enough to fill that cavity. I'll letyou know how it works after I get the jeep back on the road.
4ll. Position the clutch sleeve and 1st/Reverse gear into the neutralposition.
4mm. Place the shift tower gasket in position and install the shift tower housing withthe shift forks in the shift grooves.
4nn. Install the six screws and tighten. (The shift tower is usually removed andinstalled in the vehicle. If you are just putting the shift tower on for safe keeping donot tighten the screws. This could damage the gasket.)
Merl - Oh, and one last thing.While you've got your transmission output gear off (you've got to have it off to separateyour TC and transmission), count the number of teeth on that sucker. You never know whenyou're going to run across a used Warn OD at a decent price and wouldn't you just HATE tomiss out because you didn't know or guessed wrong?
** Rick - On the last T-90/Model18 rebuild I encountered a new problem. I installed the locking plate from the bottominstead of the top. When I bolted the T-case to the T-90, the locking plate interferedwith the mating and I had to pull it all back apart to swap the plate. Make sure you checkthis fit before applying gaskets and sealer. Another guy was rebuilding his IH Scout T-90and had the same problem. His info is printed below.
Gary- Major lesson learnedlast night. There's already some added comments in your text regarding the locking platethat secures the reverse idler shift shaft and the cluster gear shaft. On IH Scout usingthe T90/T18 combo, the locking plate MUST be installed from the top, so that it is a right-side up 'T'. I put mine in from thebottom, put gasket shellac on all the gaskets and cranked everything down tight. When Ifilled both with the requisite 6 pints of gear oil and started the engine, I had a puddleon the floor pretty quickly. Tried quick fixes like shellac on the threads of the boltsthat join the T18 and T90, but still had good flow. Took the two units apart last nightand found that the locking plate is interference with the fit. Kinda like slipping a dimebetween the mounting surfaces.
Dr. Vern-During assembly,the shaft locking plate on the rear must be correctly positioned to fit into a recess onthe front of the T-case. Rick's guide mentions this, and how one guy had the plate keepthe T90 and T-case from pulling together correctly. I used the gasket as a template andtraced the outline of the recess with a magic marker. When the two shafts were stillprotruding about an inch, that is when I fit the locking plate into the shafts' grooves.That allowed me to keep everything in correct alignment as I drove the shafts all the wayin.
Rick- Even with a correctly alignedlocking plate it is possible for the plate to interfere with the T-case installation. This will cause one of two things to happen. Either the tranny and T-casewill leak terribly through an unsealed gasket or the tranny will bind up and not turn. The binding is caused by the T-case cocking the Rear Main Bearing. Thesolution to this problem is to trim the locking plate with a file or grinder to make itfit inside the hole in the T-case.
Dr. Vern - I felt like I haddiscovered the cure for cancer or something when I finished the rebuild. It was not hardat all. It is just a matter of following the steps in the correct sequence. Being familiarwith all the names of the parts helped, too, as you read the instructions.
Dr. Vern - Since you musthave the shift tower off when removing or installing the T90, I'd suggest taping a pieceof cardboard across the open case. I think I'd cry if some crud from under the body fellin during the installation.
Rick - Here's new bitof information for you. Tom Jacoby's tranny went together beautifully and workedfine until it was bolted to the T-case. Once it was bolted up everything bound uptight and was very hard to turn. This sounds a lot like the binding locking platementioned above and therefore that was inspected and ruled out. In the end the causeof his problems stemmed from the bearing spacer being too thick (0.031') for histranny. This forced the Mainshaft forward too far when the T-case was installedagainst the tranny. On most T-90s this thick a spacer would not have been a problembut on his the other parts had larger tolerances too and they combined together to createan assembly that was too long to fit the case. If you encounter this problem you mayneed to find a thinner spacer. A new spacer that was 0.021' thick worked justfine for Tom.
OPERATIONAL CHECK
5a. Shift the tranny into reverse and rotate the main gear. On T-90s with the felt sealin the front bearing retainer you will have to use some force to rotate it. The mainshaftshould rotate in the opposite direction with no grinding or scraping sounds.
5b. Shift the tranny into first gear and rotate the main gear. The mainshaft shouldrotate in the same direction only much slower.
5c. Shift the tranny into second gear and rotate the main gear. When you do this youwill need to hold the rear bearing retainer in place or it will allow the mainshaft toslide out the back of the tranny and the pilot bearings will drop to the bottom. Thetranny should shift smoothly into second gear and the mainshaft should rotate smoothly inthe same direction.
5d. Shift the tranny into third gear. The tranny should shift smoothly into second gearand the mainshaft should rotate smoothly in the same direction.
Bob Stewart:Caution:In a November 1958 Jeep Service and Parts News, They note that there are 2different size bolts to hold the T-case to the transmission, 1' & 1 1/8'.They warn that improper assembly can lead to gear damage and leaks. They want the two1' bolts in the lower left and lower right.
Rick: I looked this warning over very carefully and I agree that installing the 11/8' bolt in the lower left corner position would damage the reverse idler gear. I was unable to find a reason for the shorter bolt in the lower right hole unlessthey were concerned about confusion as to which side was which.
ASSEMBLY CHECKLIST OF THINGS OFTEN FORGOTTEN
1. Main gear snap ring.
2. Main shaft Snap ring.
3. Clutch hub installed with larger hub forward.
4. Clutch hub sleeve installed with the shift fork groove to the rear.
5. 1st/Reverse gear installed with the shift fork groove forward.
6. Clearance for the countershaft locking plate between the cases.
7. Non hardening sealant on every bolt that penetrates to the inside of the case. I'vedecided to agree with Dr. Vern on something that he said long ago, 'RTV gasketsealers should be outlawed.' I found that stuff in every possible orifice in the lastcase I rebuilt. It was causing oil starvation to the bearings.
8. Running the Tranny through the shifts prior to installing it in the vehicle.
Thanks to Ron Cox and Reed Cary I have been able to add the Shift Tower rebuildinstructions to this guide. Without their help this would not have been possible.
DISASSEMBLY
Remove shifter fork pins from the second and high-speed shifter-fork and the low andreverse speed shifter-fork. In some shifters this is a split pin and in others it will bea hollow pin that is staked in the end. The split pins can simply be driven out with a pindrift but the staked pins must have the staked end drilled off first. Place both shiftrails into the neutral position.
The M-38 shift tower will have two 3/8-inch countersunk head pipe plugs at the rear ofthe shift rod rail holes. Remove these. For other models this is N/A.
Verify that the rods are both still in the neutral position. Drive the second andhigh-speed gears shifter rail to the front until the rail hole expansion plug can beremoved. Carefully slide the shifter rod forward while rotating the shift lever notch inthe rod toward the bottom of the tower. Do not allow the notch to pass the poppet ballwhile it is pointed toward the top or the poppet ball and spring will become trapped inthe notch. If this happens you can force the poppet ball back into the hole by rotatingthe shaft with a pair of vise-grips. Caution: as the rodslides past the poppet ball, the natural tendency is for the ball to shoot out. Cover thehole with a rag. Remove the rail and the second and high-speed gears shift fork.
Drive the low and reverse speed gears shifter rail to the front until the rail holeexpansion plug can be removed. This rail does not have the notch to worry about so itshould be a little easier to deal with. Caution: as the rodslides past the poppet ball, the natural tendency is for the ball to shoot out. Cover thehole with a rag. Remove the rail and the low and reverse speed gears shifter fork.
This leaves the removal of the shift lever. This procedure is totally different betweenthe M-38 and other T-90 transmissions.
M-38: Unscrew the shift tower cap from the shift tower and remove. Slide shift leverout of the shift tower.
Other T-90s: Turn the shift tower upside down and lock into a vise if possible. Itworked pretty well for me sitting in my lap. Start at the top of the spring and using alarge screw driver gently pry the spring over each spring retaining dog one at a time. Myfirst idea was to use a pair of vise-grips and rotate the spring from the case. This canbe done but it is very hard on the spring and chews up where the vise-grips bite. It onlytakes about 2 minutes to do it with the screwdriver and it's much easier on the spring.Once the spring is removed, slide the shift lever out the bottom of the tower.
INSPECTION
Now clean and inspect the shift tower case for cracks, stripped threads (For M-38) ordamage of any kind. Any cracked or otherwise damaged units should be replaced or repaired.
Replace the gearshift lever if it is excessively worn or bent.
M-38: Replace the gearshift shift tower cap if it is bent or has stripped threads.
Other T-90s: Replace shift lever retaining ring if it is bent or broken.
Replace the second and high speed gears shifter-rail and second and high-speed shifterfork if they are excessively worn, or if they are bent or distorted. Any burs should beremoved.
Replace the low and reverse speed gear shifter-rail and low and reverse speed shifterfork if they are excessively worn, or if they are bent or distorted. On one of the ones Iinspected, there was a groove cut in the shift rail where the poppet ball rode. Any bursshould be removed.
M-38: Replace the 3/8-inch countersunk head pipe plugs if the threads are stripped.Replace the gearshift lever support spring if it is cracked or distorted.
Replace the poppet balls and poppet ball springs if they are worn, broken, ordistorted. I recommend replacing them anyway.
ASSEMBLY
I have found that the staked pin that prevents the shift lever from rotating in thetower and the pin that allows for the installation of the interlock pin will leak if leftalone.Prior to assembly you should clean around these pins until all grease andoil are removed and then seal with a good gasket sealer and allow to cure. Make sure toforce the gasket sealer in around the pins but make sure it doesn't go all the way throughto the inside. I can attest to the fact that if you fail to do this these pins can leak alarge amount of oil. The last time I had my shift tower off Imade a few other mods to it. One mod was to drill a hole in the rear between theshift rails. I tapped threads into the hole to accept a bolt. Then I made aplate that fit over the end of the shift tower. The tail end of the shift tower hadto be filed smooth. This was easy to do by keeping the pressure applied to thecenter of the file instead of the ends. I then sealed the end of the sift rails withthis cap plate. I did have to remove about 1/4' off theend of the first/reverse shift rod to prevent it from hitting the plate. It hasn'tleaked any oil since. In addition to this modification my old shift lever had been grounddown a time or two to fit various shifter knobs. When I bought my new knob for theshifter it would not fit the current thread. I bought a grade 5 bolt with the rightthreads and cut the head off of it. Then I ground down a releaf on the bolt andshifter and MIG welded the bolt on. I oil quenched the finished product and groundit down smooth. I now have a beautiful shifter that the know screws right onto.
M-38: Install shift-lever back into the shift tower and secure with gearshift shifttower cap.
Other T-90s: Turn shift tower upside down and install shift lever into the tower makesure the positioning pin seats in the notch on the shift lever ball. Slide spring downover the shift lever and pop the spring over the retaining dogs one notch at a time with alarge screw diver. This took me about 20 minutes the first time I did it, but now I can doit in about 2 minutes. Just don't loose patience with it.
Make sure the shift lever is to the inside of the rail before installation. Insertpoppet ball spring and poppet balls into gearshift control housing on the low and reversespeed gears side. Insert the low and reverse speed gears shifter shaft into the gearshiftcontrol housing from the rear. If you have difficulty getting the shaft to go in more thanabout 3 inches inspect the interlock pin to make sure it is out of the way. Slide the lowand reverse speed gears shifter fork onto the rail Note: it is easy to put this fork onbackwards if you aren't careful. When it is properly installed the fork should fall evenlyin the middle of the shift tower. Depress the poppet ball and poppet ball spring, using ablunt shaft (Do not use a sharp tipped instrument like a screwdriver or a nail.) and slidethe rail in over the poppet ball to the second groove. This is the neutral position.
Make sure the shift lever is to the inside of this rail also before installation.Insert poppet ball spring and poppet balls into gearshift control housing on the secondand high-speed gears side. Insert the second and high-speed gears shifter rail into thegearshift control housing from the rear. If you have difficulty getting the shaft to go inmore than about 3 inches inspect the interlock pin to make sure it is out of the way. Bynow the interlock pin must fit into the detent notch in the low side rail.
Situate the shift lever so that it falls in between both the Low shift fork and theHigh shift notch. Secure both shifter forks onto the shifter shafts with shifter forkpins. For those with staked pins, flange the ends of the gearshift fork pins with a centerpunch.
M-38: Install 3/8-inch countersunk head pipe plugs in ends of gearshift controlhousing.
Place a small amount of sealant around the new gearshift rail hole expansion plugs intoshifter shaft holes in the front end of gearshift control housing. If there is enough roomin the ends of the rear shaft holes of your shifter, I recommend installing these plugsthere too.
There has also been some interest in installing a reverse light switchin the shift tower. A write-up for this can be seen here
Bruce inquired on the Bulletin Board about the different versions of the T-90 transmission. 'What is the difference between these types of T-90 Gearbox: T-90, T-90A, T-90C and T-90J. I know that there are different ratios for first gear and also that some have selectors from the side not the top and I suspect that the length of the main drive gears are different?'
Ruiz posted: 'CJ-2A, CJ-3A and M38 used the T-90A. The M38A1 used T-90A1 while the CJ-3B used either the T-90A1 or T-90C. CJ-5 and CJ-6 used T-90A or T-90C. Utility wagons and trucks used T-90A or T-90J.
'The T-90A1 and T-90C use the same case marked T-90A and are floor shift. The T-90A1 has a 15/16-inch input shaft and 18 teeth on the input gear, while the T-90C has the same size input shaft, but 16 teeth on the input gear. The T-90J has 1-1/8th input shaft with 18 teeth on the input gear and is either a column or floor shift.'
Maxx added: 'This is from Novak Adapters great website: 'All T-90 transmissions have a 1-3/8 inch, six-spline output shaft for mounting the transfer case input gear. There are three major versions of the T90 to differentiate:
T-90A1
'The T-90 used from 1946 to 1962 with the L and F-head four-cylinder engines is designated as the T90A1. These versions all feature top shifters, a seven inch input shaft (stick-out length) with 15/16ths inch, 10 splines and a felt-sealed front bearing retainer assembly. The input shaft has an 18-tooth, helically cut input gear. The cluster gear has a 33-tooth driven gear, resulting in a 2.98:1 first gear and a 1.66:1 second gear.
T-90C
'The T-90 used from used from 1963 to 1971 with the F-head four-cylinder engine is designated as the T-90C. It features top shifters, a seven inch input shaft (stick-out length) with 15/16ths inch, 10 splines and a felt-sealed front bearing retainer assembly. Since the T-90C uses a case marked 'T90A,Õ you will need assurance that the transmission in question came from a post '62 Jeep, or you will need to pull the top cover and count teeth. The T-90C has a 16-tooth, helically cut input gear. The cluster gear has a 35-tooth driven gear, resulting in a 3.44:1 first gear and a 1.85:1 second gear.
T90J
'The T-90J was used with the six-cylinder trucks from 1952 to 1965. These were either column or floor shift models. They had an ~9-1/4 inch input shaft (stick-out length) with a 10 x 1-1/8' splines and a neoprene-sealed front bearing retainer assembly. The T-90J has an 18-tooth, helically cut input gear. The cluster gear has a 33-tooth driven gear, resulting in a 2.79:1 first gear and a 1.66:1 second gear.'
Bill Coelho asked: 'Some of the information that I have gathered from various books says that there is a 2.79:1 first gear in early T-90A models and a 3.34 or 3.39:1 first in the T-90C models. Can anyone verify this as fact? If so, are the first gears interchangeable?'
Dave answered: 'The T-90 did have an optional first gear of 3.31:1 in the '60s with the 4.27 axle ratio. You can modify your T-90 if you can find the gears. What you want is the 16 tooth input shaft, and the 35 tooth cluster gear. All of the other parts are the same.'
While collecting parts to rebuild his '63 3B, Doug came across a T-90 case marked T-90E-1. 'I have been searching and searching but have not come up with any references for this T-90E-1. I have seen T-90A, C, and J, but thatÕs it. This one is a floor shift and does not mate to the Spicer 18 transfer case without an adapter. Does anyone have any information on these things?'
Andy Stock replied: 'I think that the main difference between the A, C, J, E, etc. was the gear ratios. I think that third was always 1.00:1 but first and second varied, depending on the application. Rick Grover lists on his speed calculator page an ASI-T90E with a 3.34:1 first, 1.85:1 second, and 4.53:1 reverse.'
Frank Kotyz from the Czech Republic inquired: 'What differences are there between the T-90 and T-90A1? I have two CJ-3Bs from '53 and '57 and both have the T-90A1. My manual only describes the T-90.'
Bill said: 'I think that there was a gear change from 26-tooth to 29-tooth.'
Oldtime explained: 'The correct transmission for the '53 and '57 CJ-3B is the T-90A1. That number should be easily noticed on the outer left side of the case. As Bill mentioned, you will notice a difference between these years with respect to the main drive gear. This gear mounts on the transmission main shaft, yet operates inside of the transfer case. This is accurately a transfer case part as indicated in the parts lists. The main drive gear powers the transfer case intermediate gear. The '53 should have a 26 tooth count while your '57 should have a 29 tooth count output drive gear. I believe that your service manual is designating the transmission as a model T-90 for general reference to the many possible variations. These variables are insignificant for most service applications. Not likely that the transmissions were changed as they are quite durable and easy to repair.'
Synchronized First Gear?
Chuck inquired: 'Can a T-90's first gear be made to synchronize? A Jeep buddy insists that it can be done using the T-98's second gear! He further states that the T-98 can be used as an overdrive unit by putting T-90 gears in for first through third and then having a 1:1 ratio gear put in for the T-98's fourth gear. I was under the assumption that the two were not compatible in respect to swapping gears.'
Vern replied: 'I've heard that there was a late version of the T-90 produced in South America that had a synchronized first gear. There were many other similar 3-speeds with a synchronized first, so the concept is not too difficult. In practice, many of the parts are different, such as the cluster gear, etc., making a home swap pretty tricky. Don't quote me on the existence of the South American T-90, but am pretty sure it was true.
'As far as using T-98 4-speed parts for such a swap, I just so happen to have both a T-98 and T-90 in my shop. I went out and compared the two for the swap like your friend suggested. While the differences are quite involved, here are two of the major reasons why it wouldn't work:
1) The T-90 cluster gear has straight teeth where it meshes with first gear. The second gear from a T-98 has angled teeth. There is no way that they would mesh.
2) The T-90 R-1 slider gear (1st gear) is about one inch smaller in diameter than the T-98 second gear. Even if the teeth were the same, the difference in diameter precludes doing the swap. First and third gears in the T-98 were substantially different sizes and wouldn't swap in place, either.
'I'm not well versed in later Jeep transmissions, but is it possible to swap some parts between something like a T-150 and the T-90? Maybe that is what he was thinking, if that is even possible.'
Chuck added: 'Apparently someone has rigged up a T-98 much the same way, but not exactly, as a T-90 and then used fourth gear as an overdrive. To prove his point, my buddy had a type of Scout which he claims is a four-speed with modified Jeep running gear, and darned if the thing didn't seem as if it had an overdrive! I think that he stated that the synchronized first gear was from a Scout. He wasn't able to give manufacturer of the fourth gear since he was not the builder, but the concept really has me wondering if an overdrive/ fourth gear is viable in a CJ-3B or even worth the obvious trouble.'
Vern then posted: 'Hmm, this is getting interesting. I have one idea that might explain the mystery transmission, but it requires some fairly heavy-duty modifications. International Harvester offered a 4-speed with a synchronized first gear. Many IH and Jeep drive train parts were interchangeable. I'm no expert on which model it was exactly, but think it was called the T-19A.
'The case for the T-19A was identical or nearly so to the T-18 and T-98 four-speeds. All of these 4-speeds have a case that is 11.875' long, with adapters needed on both ends. The stock T-90 is only eight inches, so the 4-speed conversion is over 5' longer with the adapters. The 4-speeds are also taller, so floorboard modifications or a body lift are required. Of course, the driveshaft lengths have to be reworked, too.
'The T-98 I have, which came from a Ford truck, has the 6.32 first gear which is definitely not synchronized. I believe that the T-19A was the only 4-speed offered in that era that had a synchronized first gear, not including car transmissions. Note that the T-19A had a first gear ratio of 4.02, a concession to the synchromesh design limits.
T90 Transmission And Transfer Case
'Now what if the mystery transmission was really a T-19A? And what if the axles had been re-geared to something like 4.27 instead of the stock 5.38? With the T-19A and re-geared axles, gears 1, 2, and 3 would have been very similar to 1,2 and 3 with a T-90 3-speed and 5.38 axles. And then when the T-19A was shifted into 4th gear, it would have felt like an overdrive because of the re-geared axles.
T90 Transmission Rebuild
'That is the only plausible explanation that I can think of for a synchronized first and 'overdriveÕ in fourth gear. On the T-90 3-speed, the input and output shafts are locked together in high gear. Likewise, both shafts are locked together in fourth gear on the T-98, T-18, T-19 and T-19A 4-speeds. Without a radical reworking of the transmission internals, I can't see how else you could get an 'overdrive' ratio from a 4-speed gearbox.


'On a slightly different note, if you are looking for an overdrive function, the Warn/Saturn unit is the easiest way to go. It literally bolts up with no other modifications needed. For what you'd spend on a T-19A, reworked drive shafts and re-geared axles, a good used Warn/Saturn OD would be much cheaper.'
Ruiz Sebastian said: 'I am from Argentina and I have never heard about T-90 complete synchronized. The 3-speed transmissions that were available here were:
1) Ford 3.03: first gear - 2.99:1; second - 1.75:1; third - 1:1, fully synchronized.
2) Chevrolet: first gear - 2.85:1; second - 1.68:1; third - 1:1, fully synchronized.
3) Dodge: first gear - 3.02:1; second - 1.76:1; third - 1:1, fully synchronized.
T90 Transmission Adapter
4) T-90.'
Thanks to all the contributors, and Doug Hoffman for editing. -- Derek Redmond
T90 Transmission Shift Tower Rebuild
Return to Tech Tips on CJ3B.info.
Visit CJ3B.info on Facebook.
CJ3B Home | Contents | Search | Links | 3A and 3B Community
Last updated 6 March 2009 by Derek Redmond redmond@cj3b.infohttps://cj3b.info/Tech/T90Variaitons.html
All content not credited and previously copyright, is copyright Derek Redmond
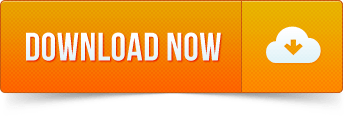